On another board this topic came up and there was a disagreement of sorts. It was said that tack welding the side of a couple bolts on your winch would help you winch stay on your bumper (stopping a wrench from fitting) and others said it would change the properties of the bolt and make them brittle as to help the winch become airborne.
So, took it upon myself to do a little research project. I am a maintenance mechanic and three of the machines I'm responsible for are heat treating. Two ionic nitriding and one vacuum carburizing. I do not claim to be a metallurgist but I recruited the help of one.
I took 4 bolts of the same size. 1 grade 5 and 3 grade 8's
Put a tack weld on the head of one grade 8 and turned up the heat on the Miller 251 I was using and melted the head on another grade 8 and water quenched it. The other two are for reference.
I then took them to the Indentron hardness tester. For those that don't know, hardness is measured in rockwell. The higher the number the harder it is. Too hard and it becomes brittle. Result are rounded for simplicity. Welds are on top of the head to make them easier to test and measurements were taken on the flats near the weld and opposite the weld.
Grade 5....................................29r
Grade 8 no weld.......................31r
Grade 8 tacked........................31r opposite weld, 32r near weld
Grade 8 Melted and quenched..31r opposite weld, 35r near weld
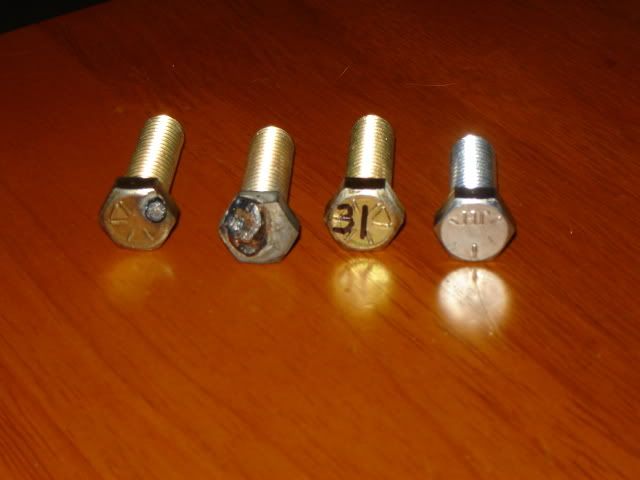
After doing this, I can say that tacking it enough to stop a wrench will not change the properties of the bolt enough to make a difference and the part that is affected is nowhere near the shaft or threads. Just don't quench it or go nuts with the weld.